Remote Control and Monitoring over the Internet - Wireless Construction Site
by Leila Rannanjärvi
At the 'wireless construction site' trucks and bucket loaders complete transportation tasks cooperatively. The truck drivers send acknowledgements to the work-site server when a transportation task has been completed. The loaders send messages to the server after each loading event. This system enables the real-time management of trucks, bucket loaders, loads and even material administration. The driving force in this case is in the expected saving, since no material is lost and there is no need for extra kilometres or work hours to be charged.
This case is not a typical Internet application, because it focuses on enhanced production and not on entertainment or context sharing. The communication is more peer-to-peer and the system is a typical nomadic system. Nomadic systems are based on a core of fixed routers, switches and hosts; at the periphery of this fixed network, base stations with wireless communication capabilities control message traffic to and from dynamic configurations of mobile hosts. Nomadic distributed systems sit in between traditional fixed networks and ad-hoc networks.
Wireless Construction Site
Together with communication technology, modern software development enables the integration of previously totally isolated work machines into the expanding global Internet and mobile communication community.
With this vision in mind, we started a project called 'Wireless Construction Site' with Finnish industrial partners. On this first-tier solution the main added value will be found in:
- accumulated information of transportation tasks containing information about the truck, the driver, the load and the driving distance
- accumulated information on loading tasks containing information about the bucket loader, the loader (the operator of the bucket loader) and the load (material and volume)
- quality 3D information about the tasks carried out by the road construction machinery.
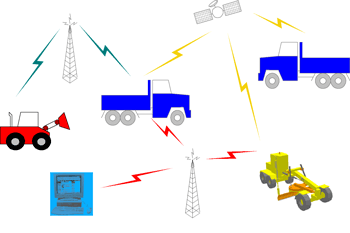 |
Figure 1: Vision of the wireless construction site. |
With this information the administration of materials, work machines (trucks, bucket loaders, road scrapers) and drivers becomes easier and more punctual! The vision includes various kinds of work machines, localisation by GPS or by GSM cell location and different communication modes depending on the available network and the current work phase (Figure 1). If no operator network is available in the gravel pit, either the machines must save pending messages or a local license-free network has to be established. Messages will be sent to the server using GPRS network and http messages. We want to test the usability of mobile phones at the work site, because the investment is lower than in the case of an in-vehicle PC. In most cases the driver already has a mobile phone, so adaptation to a newer mobile phone is easier than to an in-vehicle PC.
The wireless construction site application has three types of user roles: the driver, the contractor and the site foreman.
The driver has the mobile application in his mobile phone (or in the in-vehicle PC). He receives the transportation task from the site foreman and starts driving. When his truck enters the depot, he orders the load and the bucket loader commences loading. When the load is on truck, the loader sends the load message to the server. The message contains information about the truck, the load volume, the material loaded, the position of the bucket loader and the loading time. When the driver unloads, the unload message will be sent to the server. It contains information about the load, the unloading position and time. The localisation of truck must be transparent. Both GPS and GSM cell location methods are possible.
The site foreman allocates tasks to drivers, trucks and bucket loaders with an Intranet application running in a browser on a PC. The user identification and password will of course be checked beforehand. The server is able to combine the information for materials administration from the load and unload messages.
For the contractor an Extranet interface provides the information about trucks and work machines (hours, kilometres and tonnes), drivers and materials. Access is tightly restricted to contractor's own tasks.
There is also the server software, which contains the core wireless construction site database and also the service for database access (Web server, html form pages, WAP server and servlets). Between the Extranet user and the server is of course a firewall.
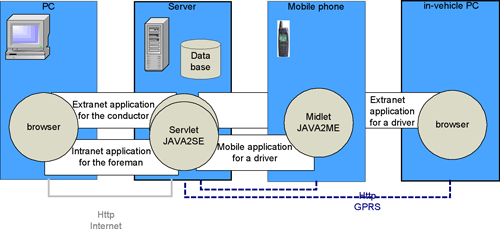 |
Figure 2: Implementation architecture of the wireless constriction site. |
Figure 2 describes the implementation architecture. The application for the driver is a midlet developed by Java2ME Wireless toolkit. The midlet is downloaded from the WAP server and saved into the mobile phone. The mobile phone must support Java, ie contain a Java K virtual machine and CLDC (Connected Limited Device Configuration) allowing external midlets. We are currently using Nokia 6310i phone. The carrier is GPRS and the protocol is http.
The protocol between the server and Extranet or Intranet applications is also http. The Intranet application implies direct hard-wired connection to the server as the Extranet application may be used from an in-vehicle PC. In both cases access is limited. The server allows only http protocols and the contractor or the site foreman has a set of forms that make up the database interface. The database communicates with the users only through these http forms.
The wireless construction site vision has been described and the first experiments with mobile phone and server completed. When the driver uses a midlet in a GPRS phone, he can send messages to the servlet in the server. The application development is ongoing and experimental use with several trucks and bucket loaders will take place in north Finland during spring 2003.
Please contact:
Leila Rannanjärvi, VTT
Tel: +358 8 551 2314
E-mail: Leila.Rannanjarvi@vtt.fi
|